가공 속성을 정의하는 중요한 목적은 가공법들을 구분하는 특징을 발견하고, 선별과정을 거쳐 선택할 수 있게 하고자 한다.
앞으로 설명될 3가지의 가공의군, 즉 형상화, 접합 및 표면처리는 각각 그것대로의 특징적인 속성을 가지고 있다. 또한 정해진 가공법의 물리적 한계와 가공속도의 한계에서 생산된 재료의 물성을 평가방법을 분석하는 것도 흥미 있는 일이다.
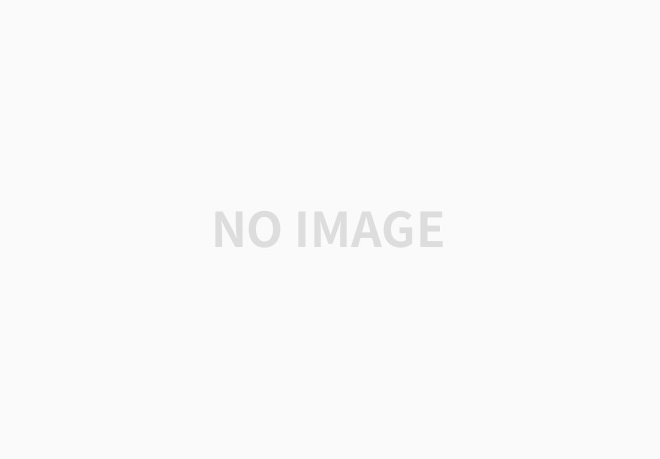
재료- 가공 적합성
특정 재료를 명시하면 어떤 가공법은 금방 선정과정에서 제거할 수 있다. 혹은 반대로 재료의 선정이 선별과정이 된다. 형상화는 일반적으로 녹임 혹은 연화로 쉬워지는데 각 재료별 융용온도는 많이 다르다. 약간의 중복이 있지만, 분말가공의 경우 금속 및 세라믹이 같이 사용되고, 유리와 고분자는 성형할 수 있다. 형상화에 사용되는 기계가공의 모든 재료에 적합하다. 접착제 혹은 잠그개 사용하는 접합 공정은 매우 다양하고 대부분의 재료와 함께 사용된다. 단, 용접은 정해진 재료에만 사용된다. 마감공정은 특히 금속 같은 강한 재료에 많이 사용되고, 고분자 재료는 형상에 따라 성형 후에 특별한 마감 이외에는 추가 작업은 없다.
재료 선택 및 가공 선택의 조화
재료 및 가공의 선택은 밀접한 관계가 있다. 가공법의 선택이 재료선택과 연관된다. 예로 만약 알루미늄 합금이 처음 재료선택과정에서, 주물이 가공법으로 선정되면, 알루미늄합금의 일부만이 주물공정에 사용 될수 있다. 만약 부품이 열처리과정에서 시효경화된다면 재료의 선정은 열처리가 가능한 알루미늄 주물 합금뿐이다. 따라서 우리는 계속해서 가공과 재료를 고려해야 하고 맞지 않는 결합은 피해야 한다.
중요한 것은 재료 혹은 가공법의 선정에서 다른 것을 고려한지 않고 하나를 선정하면 안 된다는 것이다.
일단 처음 선별이 통과되면 상호 선택과정을 거쳐야 한다.
형상화 공정 : 속성 및 시작
크기 및 부분 두께의 물리적 한계
가공 시에 부품의 크기에는 한계가 있다. 주물 및 성형은 액체 혹은 반액체 상태의 재료 흐름에 달려 있다. 부분 두께의 하부한계는 유동의 운동에 의해 결정된다. 점도 및 표면 장력은 좁은 도관의 흐름을 방해한다. 또 얇은 부분의 큰 표면에 의한 열손실은 흐르는 재료를 냉각시키고, 도관이 채워지기 전에 점도를 증가시킨다. 고분자 및 유리의 점도는 온도가 하강함에 따라 꾸준히 증가한다.
순수 금속은 일정한 온도에서나 고체화되는데 점도는 단계적으로 증가한다. 하지만 합금은 어느 범위의 온도에서 일어나며 '죽 영역' 이다. 이때 합금은 일부는 액체, 일부는 고체 상태이다. 이 영역의 넓이는 온도, 몇 도 혹은 몇백 도의 차이를 갖는데 금속 주물의 흐름은 합금의 성분에 달려 있다. 일반적으로 고압다이캐스팅 및 성형방법은 얇은 부분을 만들 수 있지만 장비가격은 높다. 빨리 생산하면 더 많은 난류흐름으로 많은 기공이 생기며 금형도 손상을 입을 수 있다.
주물 및 성형 시에 부분 및 크기의 상부한계는 수축의 문제에 의해 결정된다. 주물 및 성형물의 표면은 가장 먼저 식고 고체가 되며 단단한 표면이 된다. 내부가 후에 결정화할때 부피의 변화는 제품을 뒤틀리게, 표면에 크랙이나 내부 기공을 형성한다.
이러한 문제는 형상의 변화가 있는 곳에서 가장 심하다. 억압은 인장응력을 가져오고 열에 의한 찢어짐과 억제된 열수축에 의한 균열의 원인이 된다. 다른 성분은 다른 형태의 열 찢어짐을 보이는데 이는 재료, 가공법 및 설계의 세밀한 조화를 보여준다.
주물 및 성형 가공 시에 대부분의 자료는 설계할 때 결함을 피하기 위한 원하는 단면을 달성하기 위한 부품의 형상 및 금형의 치수의 지침에 관한 것이다. 부품의 형상이 정해진 경우 금형에 유입되는 '금형 통로' 및 남은 재료 혹은 공기가 빠져 있을 '구멍'의 위치 선정이 자유롭다.
금속 및 세라믹의 분말 공법 역시 유동에 달려 있다. 분말로 금형을 채우는 것은 중력에 의한 자유유동 및 분말을 밑으로 흐르게 하는 진동을 이용 균일한 충진을 완성한다. 다음은 압축(냉 채움)을 하게 된다. 충진 후에 금형은 열을 가해 소결을 통한 혹은 일정한 압력의 열등압을 통해 고밀도화 한다. 변형에 의한 금속 형상화, 예로 열 및 냉간압연, 단조 혹은 압출도 유동이 관련되어 있다. 고체 금속은 소성변형 혹은 크립에 의해 유동된다.
대부분의 형상화는 고온의 항복강도는 실온에서의 것보다 낮기 떄문에 고온에서 하게 된다. 이때 실온에서 변형 시 생기는 항복강도의 증가, 즉 가공경화 현상이 없기 때문이다. 압연, 단도, 압출 시 얻을 수 있는 가장 얇은 두께는 소성 유동에 의해 결정되며 이는 주물공정 시 얻어지는 얇은 두께가 점도에 의해 결정되는 것과 같은 원리이다.
극소형 혹은 박판 물건- 극한적 추구
그렇다면 어떻게 극소형 물건을 만들 것인가?
확실한 방법은 큰 것을 잘라서 만드는 것이다. 즉 가공하는 것인데 돌림, 형상, 드릴링 그리고 밀링이다. 크기의 상부한계는 기계를 구입할 수 있는 예산과 그 기계를 돌릴 수 있는 전기 값에 의해 결정된다.
소형의 한계, 여기서는 밀리그램 혹은 몇 분의 1mm는 기계의 탄력성 및 재료에 달려 있다.
연속형상 가공인 압연은 부엌에서 사용 중인 알루미늄 호일 두께 정도까지 생산할 수 있다. 포일은 압연 봉에 들어가서 나갈 때까지 항복하고 얇아진다. 큰 상호비 및 마찰 한계는 철 압연 봉이 탄성적으로 평평하게 될 정도의 큰 압력이다. 이 공정은 두 개의 얇은 판을, 중간에 윤활제를 넣어 작업 후 분리를 쉽게 한다. 동시에 공급하는 통합 압연으로 쉽게 할 수 있다. 부엌에서 사용하는 포일이 압연봉과 접촉하는 한쪽은 빛나고 다른 쪽은 흐린 이유이다.
만약 더욱 작게 만들고 싶다면 유동은 더이상 불필요하다. 그 부분은 너무 얇아 가공하려고 하면 구부려진다. 이때는 화학적 방법을 사용한다. 일반적인 화학공정, 즉 에칭, 화학적 밀링, 전자-방전 밀링은 정밀 가공 때의 크기와 같은 특징이 가능하다. 진짜로 작은 것을 만들려면 전자기 생산에 사용되는 읽기, 프린팅 및 에칭 기술이 필요하다. 현재 사용되는 재료인 실리콘에 기초한 기술에 의해 제약되고 있으며 현재 에어백의 터짐 방아쇠 같은 상업적 장치는 이렇게 만들어지고 있다.
'재료과학' 카테고리의 다른 글
재료의 요리법 - 공정과 특성에 대하여 (0) | 2024.01.04 |
---|---|
재료 가공에 중요한 속성에 대해 알아보자 (0) | 2024.01.04 |
설계시 가공법을 선정하는 것에 대해서 (0) | 2024.01.03 |
재료 공정 설계의 전략에 대해서 (0) | 2024.01.03 |
재료과학의 설계공정에 대해서 (0) | 2024.01.03 |